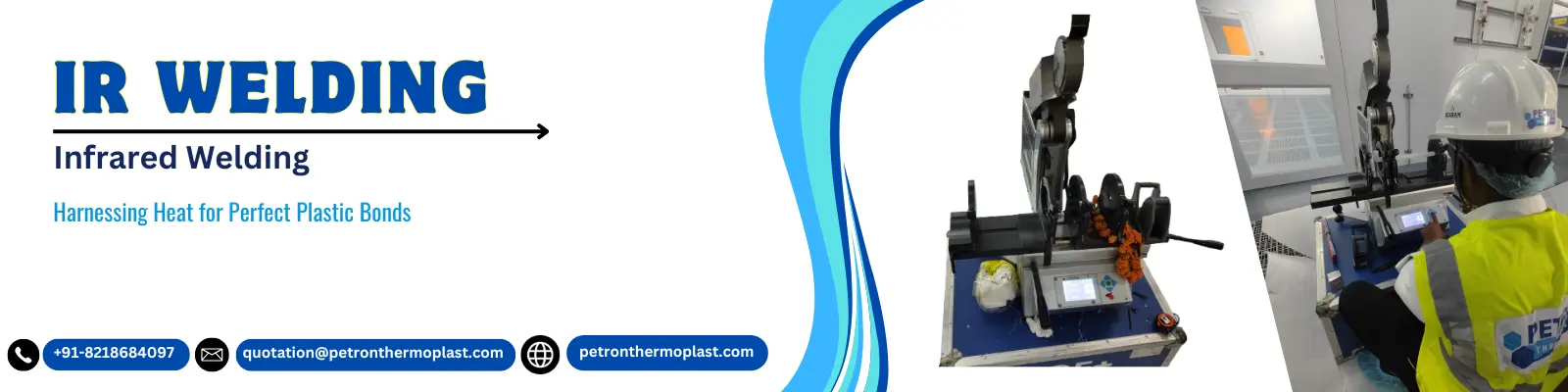
What is Infrared (IR) Welding?
Infrared welding is an advanced plastic welding technique that uses infrared radiation to heat and join thermoplastic materials with precision and efficiency. This non-contact process involves directing infrared energy onto the joining surfaces, causing the plastic to soften before pressing the parts together to form a seamless, durable bond. Known for its ability to deliver strong, clean, and aesthetically pleasing joints, infrared welding is widely used in industries such as automotive, medical devices, electronics, and consumer goods. It offers numerous advantages, including fast processing times, high precision, and no need for adhesives or solvents, making it both efficient and environmentally friendly. While it requires specialized equipment and is limited to compatible thermoplastics, infrared welding remains a preferred choice for applications requiring robust and reliable connections.
Process of Infrared (IR) Welding
Infrared Welding (IR Welding) is a precise and efficient method for joining thermoplastic components. The process involves using infrared radiation to heat the plastic surfaces without direct contact, followed by applying pressure to form a strong, durable bond. Below is a step-by-step outline of the IR welding process:
1. Preparation
- The thermoplastic components to be welded are cleaned to remove contaminants like dust, grease, or moisture that could interfere with the welding process.
- The parts are securely positioned in fixtures to ensure proper alignment during the welding process.
2. Heating
- An infrared emitter, such as a lamp or panel, is positioned near the surfaces to be joined.
- Infrared radiation is directed at the surfaces, causing the plastic to absorb heat and soften.
- The heating parameters, such as time, temperature, and distance, are precisely controlled to achieve optimal softening without degradation.
3. Removal of Infrared Source
Once the desired heat level is achieved, the infrared emitter is retracted to prevent overheating and deformation of the parts.
4. Pressing and Joining
- The softened surfaces are pressed together under a controlled pressure.
- The molten materials flow and intermingle, creating a bond at the molecular level.
5. Cooling
- The joined parts are held in position while they cool and solidify.
- The cooling process is critical to ensure the weld is strong and maintains the desired shape.
6. Inspection and Finishing
- The welded part is inspected for quality, ensuring that the bond is uniform, strong, and free from defects such as gaps or misalignment.
- Any excess material (flash) is trimmed if necessary.
IR Welding Machine
An Infrared Welding Machine is a specialized piece of equipment designed to join thermoplastic materials using infrared radiation. These machines use infrared emitters, such as lamps or panels, to heat the joining surfaces of the plastic components without direct contact. Once the surfaces are sufficiently heated and softened, the machine presses the parts together under controlled pressure, forming a strong and precise bond upon cooling.
These machines provide a clean, fast, and efficient solution for joining plastics, eliminating the need for adhesives or solvents. They ensure high-quality welds, making them an essential tool for industries that demand precision and durability.
Infrared (IR) Welding Applications
Infrared welding is a versatile and precise technique widely used in various industries for joining thermoplastic components. Its ability to produce strong, clean, and reliable bonds without adhesives or solvents makes it ideal for a range of applications:
1. Automotive Industry:
Welding components like fluid reservoirs, air intake manifolds, instrument panels, and lighting assemblies.
2. Medical Devices:
Assembling fluid containers, surgical instruments, and other sterile products with precise and clean welds.
3. Electronics:
Enclosures for sensitive devices, battery casings, and connectors where reliability and aesthetics are critical.
4. Consumer Goods:
Welding of durable plastic parts in appliances, toys, and household products.
5. Packaging:
Sealing plastic containers, blisters, and caps for secure and tamper-proof packaging.
6. Industrial Equipment:
Joining components in machines and tools, such as housings and fluid conduits.
Time & Absorption
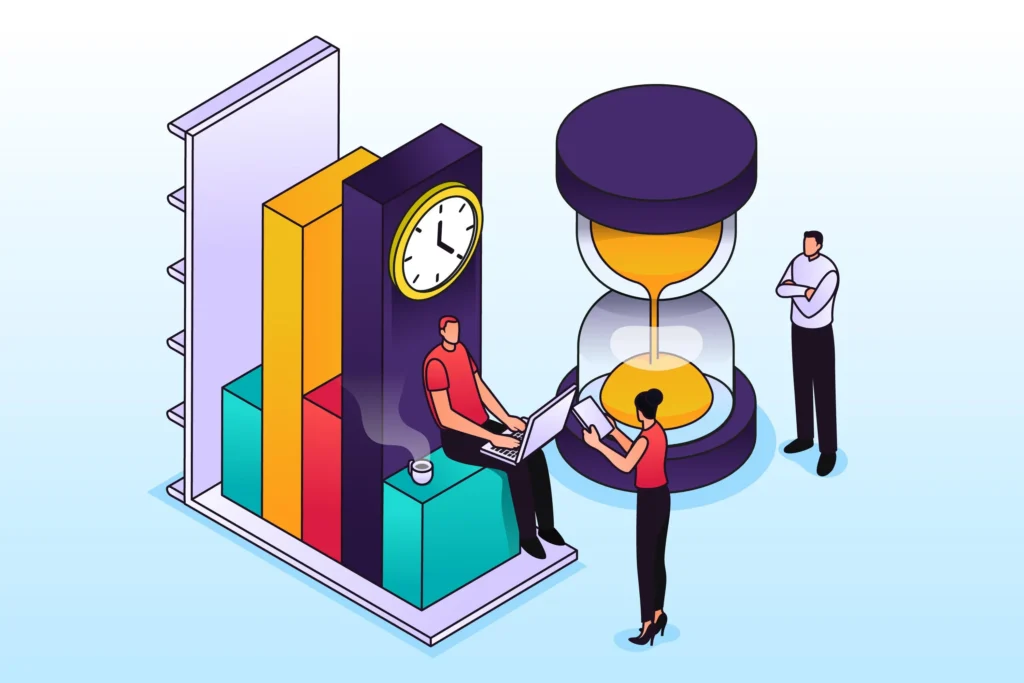
1. Time in Infrared Welding
The total duration of the welding cycle, particularly the time during which the infrared radiation heats the material and the pressing time for joining.
Key Phases Involving Time:
- Heating Time
- Pressing Time
- Cooling Time
2. Absorption in Infrared Welding
The ability of the plastic material to absorb infrared radiation, converting it into heat.
Factors Affecting Absorption:
- Material Type
- Surface Characteristics
- Wavelength of Infrared Radiation
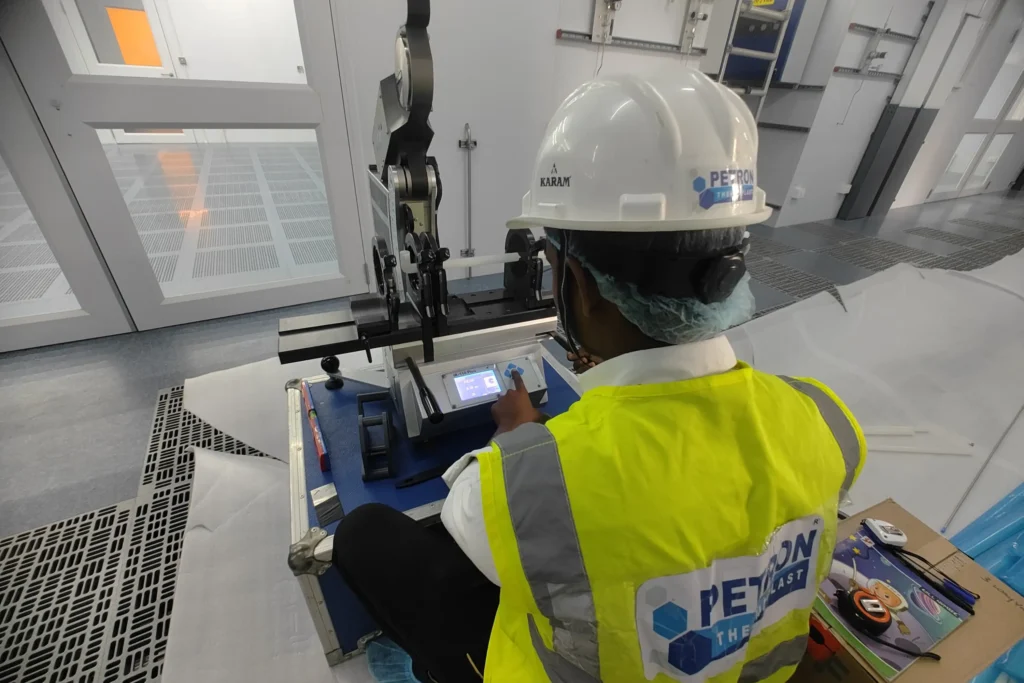
Critical Infrared Parameters
- Heating Temperature
- Heating Time
- Distance Between Emitter and Part
- Pressure During Joining
- Cooling Time and Rate
- Material Properties
- Infrared Wavelength
- Alignment and Fixturing
Factors Affecting Proper Welds
- Material Properties
- Infrared Heating Parameters
- Surface Preparation
- Pressure During Joining
- Cooling Time and Rate
- Alignment and Fixturing
- Equipment and Tooling
- Environmental Conditions
- Operator Skill and Setup
Infrared Welding Products
Infrared welding is used to produce a wide range of thermoplastic products that require precise, clean, and durable bonds. Below is a list of common products across various industries:
1. Automotive Products
- Air intake manifolds
- Fluid reservoirs (coolant, washer fluid tanks)
- Fuel system components
- HVAC ducts and vents
- Lighting assemblies (headlight and taillight housings)
- Instrument panels and control systems
2. Medical Devices
- IV fluid containers
- Surgical instrument handles
- Catheter components
- Diagnostic equipment housings
- Pharmaceutical blister packs
3. Electronics
- Battery housings
- Connectors and cable assemblies
- Sensor enclosures
- Control panel casings
- Device housings for consumer electronics
4. Consumer Goods
- Plastic water bottles and thermos flasks
- Storage containers and lids
- Toys with multiple plastic parts
- Appliance housings (e.g., vacuum cleaners, kitchen appliances)
5. Industrial Components
- Machine housings
- Plastic conduits and fluid transport systems
- Sealed containers for hazardous materials
- Custom enclosures for industrial tools
6. Packaging Products
- Plastic caps and closures
- Blister packs for retail products
- Tamper-proof seals and containers
7. Aerospace Components
- Fluid and air handling ducts
- Lightweight structural parts
- Electronic system housings
Infrared Emitter Systems
Infrared emitter systems are the core components in infrared welding, responsible for generating and directing infrared radiation to heat thermoplastic materials for welding. These systems are designed for precision, efficiency, and adaptability to a range of applications.
Types of Infrared Emitters
- Short-Wave Emitters
- Medium-Wave Emitters
- Long Wave Emitters
Advantages of Infrared Welding
Infrared welding offers several key benefits that make it a preferred method for joining thermoplastic materials in various industries:
1. Precise and Controlled Heating:
Allows for localized and uniform heating, ensuring high-quality welds without overheating or material degradation.
2. No Need for Solvents or Adhesives:
A clean, environmentally friendly process that avoids the use of chemicals or adhesives, reducing contamination risks.
3. High Speed and Efficiency:
Fast heating and cooling cycles reduce production time, increasing overall efficiency and throughput.
4. Minimal Distortion:
Controlled temperature application reduces the risk of warping or dimensional changes in the welded parts.
5. Energy Efficiency:
Infrared radiation is absorbed directly by the material, minimizing energy wastage and enhancing process efficiency.
6. Suitable for Complex Geometries:
Ideal for welding intricate or hard-to-reach areas, providing flexibility in part design.
7. Strong, Durable Joints:
Results in robust and reliable welds with high strength, making it suitable for demanding applications in automotive, medical, and electronics industries.
8. Automation-Friendly:
Easily integrated with automated systems, improving scalability and consistency in high-volume manufacturing.
Infrared Welding Controls
Infrared welding controls are essential for ensuring the precision, consistency, and quality of welds in thermoplastic joining. These controls regulate the critical parameters involved in the process, enabling manufacturers to achieve optimal welding results. Below are the key aspects of infrared welding controls:
- Temperature Control
- Heating Time Control
- Distance Control
- Pressure Control
- Alignment Control
- Cooling Control
- Process Monitoring and Feedback
- User Interface and Automation
Material Considerations in Infrared Welding
When selecting materials for infrared welding, several factors must be taken into account to ensure optimal performance and successful bonding. These considerations affect the efficiency, quality, and strength of the welds. Below are the key material considerations for infrared welding:
1. Material Type
Polypropylene (PP), Polyethylene (PE), Polycarbonate Sheet, Polyamide (PA), Acrylic (PMMA), (PET), PEEK and UHMWPE.
2. Absorption Characteristics
- Infrared Radiation Absorption
- Thermal Sensitivity
3. Material Thickness
- Thicker Materials
- Thin Materials
4. Surface Finish and Condition
- Surface Quality
- Surface Preparation
5. Material Compatibility
Materials with similar thermal properties and melt flow characteristics are easier to weld together.
6. Color and Pigmentation
The color of the material significantly affects its absorption of infrared radiation. Darker materials absorb more heat and weld more efficiently.
7. Chemical Composition
- Materials containing fillers or additives may have altered thermal properties, affecting how they absorb infrared energy.
- It is essential to consider the composition of the material, as some additives may interfere with the bonding process.
8. Thermal Conductivity
- Materials with high thermal conductivity spread heat more evenly, while materials with low conductivity may experience uneven heating.
- For non-uniform materials, careful control of heating time and intensity is essential to avoid weld defects.
9. Environmental Resistance
- In applications like automotive or medical industries, materials may need to resist extreme conditions (e.g., high temperatures, chemicals, moisture).
- Materials like PEEK and UHMWPE offer excellent resistance to heat, wear, and chemicals, making them ideal for demanding environments.
Final Summary
Infrared welding is a highly effective and versatile method for joining thermoplastic materials, offering precision, speed, and energy efficiency. The process utilizes infrared radiation to heat materials to their melting point, allowing them to bond without the need for adhesives or solvents.
In conclusion, infrared welding represents a superior solution for joining thermoplastics in many manufacturing sectors. Its ability to deliver clean, precise, and strong welds with minimal environmental impact makes it an invaluable tool for modern production. With careful material selection and process control, Petron Thermoplast offers a reliable and efficient method for creating high-quality products.